In the dynamic world of the automotive industry, technological advancements are continually shaping the future of vehicle design, manufacturing, and maintenance. One of the most transformative technologies in recent years is 3D printing. This innovative process has the potential to revolutionize the automotive sector in numerous ways. Let’s explore how 3D printing can support the automotive industry.
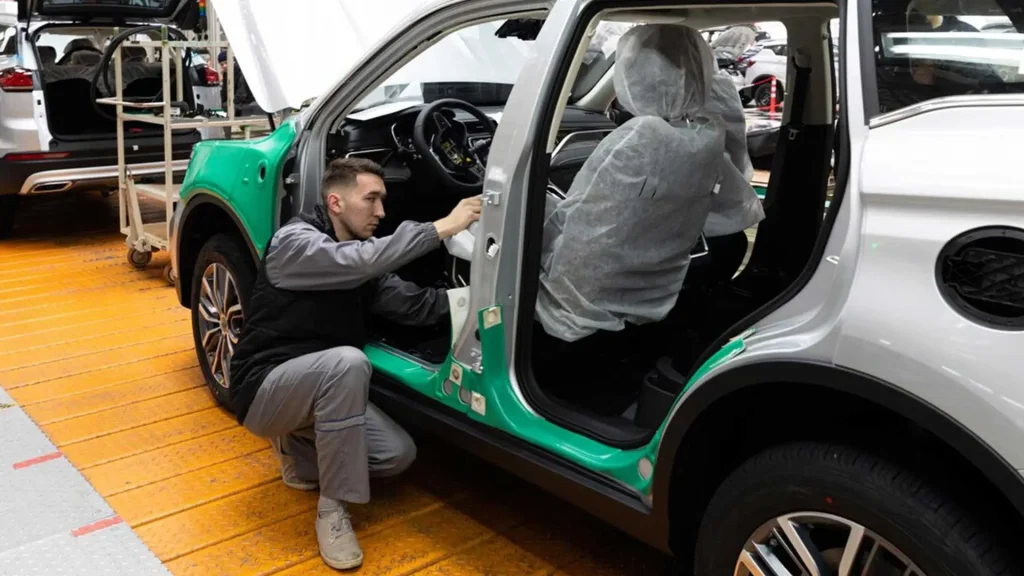
Accelerated Prototyping and Cost Efficiency
3D printing enables rapid prototyping, allowing automotive manufacturers to quickly produce and test new designs. This technology significantly reduces the time required to go from concept to functional prototype, fostering a more agile and responsive development process. With 3D printing, design iterations can be made swiftly, helping engineers and designers to refine their ideas without the lengthy wait times associated with traditional manufacturing methods.
The traditional manufacturing of automotive components involves expensive tooling and molds, which can be particularly costly for small production runs. 3D printing eliminates the need for these costly tools, enabling more cost-effective production of parts, especially for low-volume or custom projects. This reduction in production costs can be passed on to consumers, making vehicles more affordable.
Customization and Personalization
Today’s consumers increasingly demand personalized and customized products. 3D printing provides the flexibility to create custom parts tailored to individual preferences and specifications. Whether it’s a unique interior component or a custom exterior design, 3D printing allows for a high degree of customization without the need for extensive retooling.
3D printing can significantly streamline the supply chain by enabling on-demand production of parts. This reduces the need for large inventories and minimizes the risk of supply chain disruptions. Automotive manufacturers can produce parts as needed, reducing lead times and increasing efficiency.
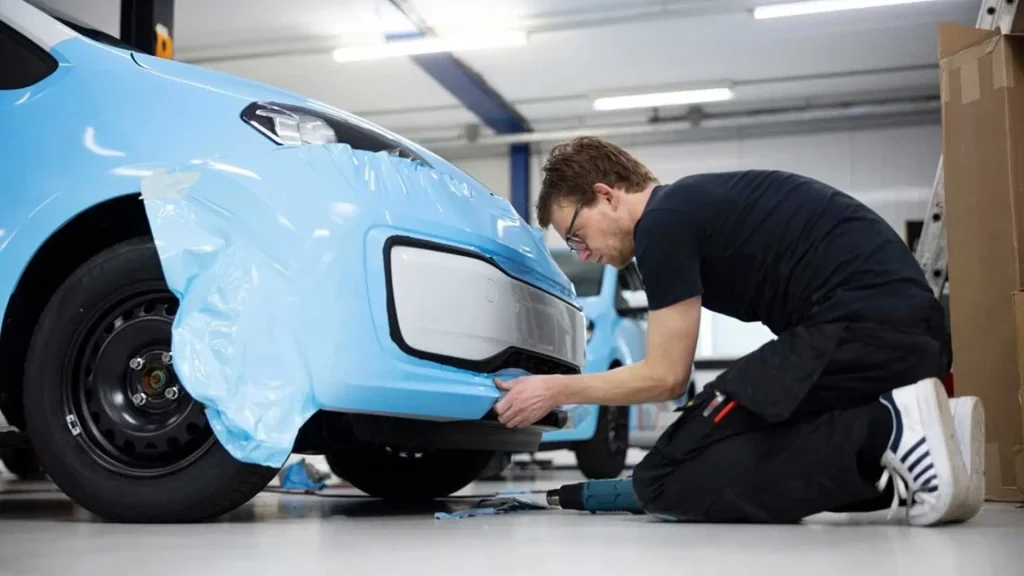
Enhanced Performance and Lightweighting

One of the critical advantages of 3D printing is the ability to create complex, lightweight structures that would be difficult or impossible to achieve with traditional manufacturing methods. These lightweight components can enhance vehicle performance by reducing overall weight, leading to improved fuel efficiency and handling.
3D printing technology continues to evolve, with advancements in materials playing a significant role. Automotive manufacturers can now use a wide range of materials, including high-strength plastics, metals, and composites, to create parts that meet specific performance criteria. This flexibility in material selection opens up new possibilities for innovation in vehicle design and engineering.
Sustainability
As the automotive industry strives to become more sustainable, 3D printing offers several environmental benefits. By reducing material waste and enabling more efficient use of resources, 3D printing can contribute to greener manufacturing processes. Additionally, the ability to produce parts locally can reduce the carbon footprint associated with transportation and logistics.
The integration of 3D printing into the automotive industry is poised to drive significant advancements in how vehicles are designed, manufactured, and maintained. From rapid prototyping and cost efficiency to customization and supply chain optimization, the benefits of 3D printing are vast and transformative. As this technology continues to evolve, its impact on the automotive sector will only grow, paving the way for a more innovative, efficient, and sustainable future.
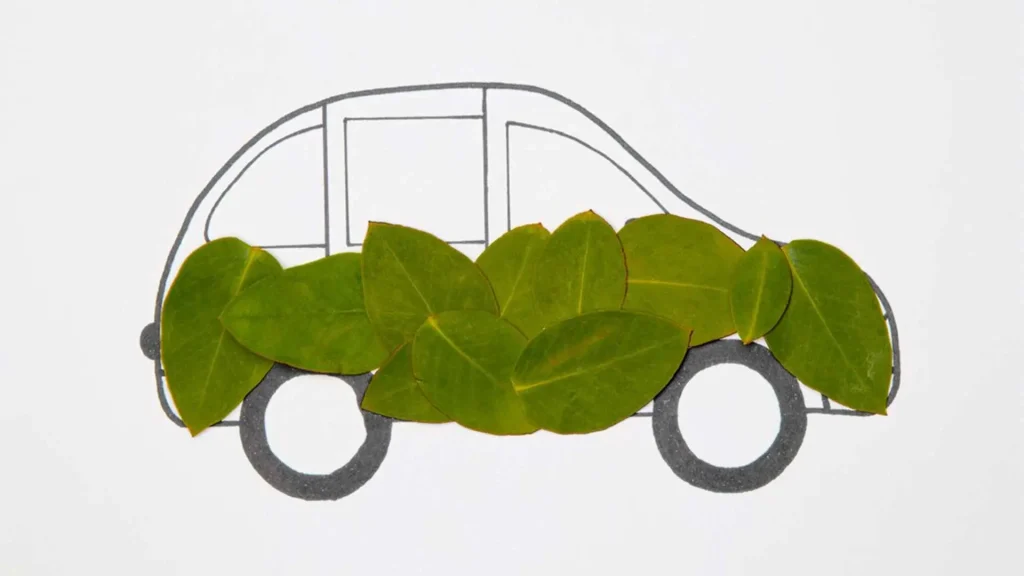